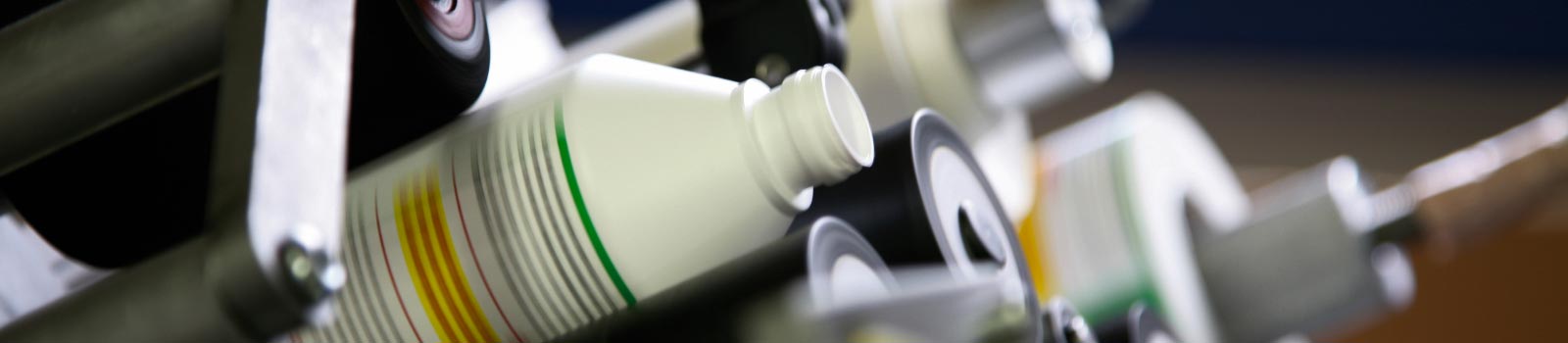
Tube packaging plays a key role in certain industries, such as the automotive and DIY sectors, and the way these products are packaged and presented to the end consumer has a major influence on their perception and choice of purchase. Tube filling is more than just filling a tube. It's a meticulous, technical process that has evolved over the years to meet the growing needs of various industries. In this article, we delve into the heart of this specialty, covering its history, innovations and the different types of tube used today.
The basics of tube packaging
Tube packaging is not a recent invention. For decades, industries have recognized the value of tubes for the efficient preservation and distribution of their products. But what do we really know about this process?
- History and development: The first tubes were mainly made of metal, and were used to package products such as toothpaste. Over time, materials and techniques have evolved, enabling a greater diversity of uses and better product preservation.
- Different filling methods: Depending on the nature of the product, whether liquid, pasty or semi-solid, tube filling methods vary. Some require high-pressure machines, while others favor precision over volume.
- Commonly used materials: Today, several materials are available for packaging, from the traditional aluminum tube to the more modern plastic tube, via the laminated tube, recognized for its strength and ability to combine the advantages of different materials. But there's also the eco-responsible tube, which is gaining in popularity thanks to its composition of sustainable materials.
Innovations in tube packaging
The world of tube packaging is far from static. With technological advances and changing consumer demands, the industry is continually striving to innovate to improve process efficiency and quality.
- Latest techniques and machines: New technologies have enabled the emergence of faster, more precise and adaptive machines. These machines can handle a variety of products, from the most fluid to the most viscous, while guaranteeing perfect filling homogeneity.
- Automation and artificial intelligence: Automation has played a crucial role in the standardization of tube filling. What's more, with the integration of artificial intelligence, machines can now instantly detect and correct errors, reducing waste and improving overall quality.
- Sustainability and eco-innovation: In a world increasingly conscious of environmental impact, machines are designed to be more eco-responsible. This translates into reduced energy consumption, less waste and the use of recycled or biodegradable materials, such as eco-responsible tubing.
Tube types: aluminum, plastic, laminated and eco-responsible
The choice of packaging material is essential. It determines not only the product's aesthetic appearance, but also its durability, shelf life and environmental impact. In this section, we explore the characteristics of the four main types of tube used in the industry.
- Aluminum tube: Historically popular, aluminum tubes are renowned for their robustness and ability to effectively protect contents from air and light. It's a preferred option for products that need a solid barrier against external contaminants, such as medical ointments or certain cosmetics. However, its environmental impact and recyclability may be cause for concern.
- Plastic tubing: Lighter and often less expensive to produce, plastic tubing has gained in popularity. It offers design flexibility, can be transparent and is generally easier to press, which is advantageous for the consumer. However, questions of durability and ecological impact remain, depending on the type of plastic used.
- Eco-responsible tubes: In the face of growing concern for the environment, eco-responsible tubes are emerging as an innovative alternative. Made from biodegradable materials or from renewable resources, these tubes seek to minimize the carbon footprint while guaranteeing product protection and preservation. They respond to growing consumer demand for packaging solutions that are more respectful of the planet.
- Laminated tubing: An innovative packaging alternative is laminated tubing. Composed of multiple layers, often a combination of plastic and aluminum, this tube offers an excellent barrier against contaminants, air and light. What's more, its multi-layer design promotes better preservation of contents. In terms of aesthetics, it enables superior printing, making the finished product more attractive to consumers.
Certifications and quality standards: the guarantee of a controlled process
In the world of tube packaging, the guarantee of impeccable quality is essential. More than just labels, ISO 9001 and ECOVADIS certifications are the pillars of our commitment to excellence.
- ISO 9001 certification: Recognized worldwide, ISO 9001 certification attests to a company's commitment to offering consistent quality to its customers. Since 2003, our QSE management has been validated by this certification, testifying to the rigor and methodology applied at every stage of the tube packaging process. It implies a continuous improvement approach, focused on customer satisfaction and the efficiency of the quality management system.
- ECOVADIS assessment: Beyond mere quality, it is essential to consider the environmental and social impact of companies. This is where the ECOVADIS assessment comes in. By assessing companies' CSR (Corporate Social Responsibility) performance, it provides a clear picture of their commitment to sustainable development. Our CSR performance has been recognized by ECOVADIS, guaranteeing our customers and partners an approach that respects the environment and high social standards.
The combination of these two awards reflects not only technical expertise, but also corporate ethics, positioning tube packaging as a committed and responsible sector.
The future of tube packaging
Tube packaging is more than just an industrial process. It's a combination of know-how, innovation and commitment to quality and sustainability. From the humble aluminum tube of yesteryear to the eco-responsible innovations of today, this industry has come a long way. In a world where ecological awareness and the demand for quality are increasingly prevalent, tube packaging is ready to meet tomorrow's challenges, combining technical expertise, responsibility and adaptation to market needs.