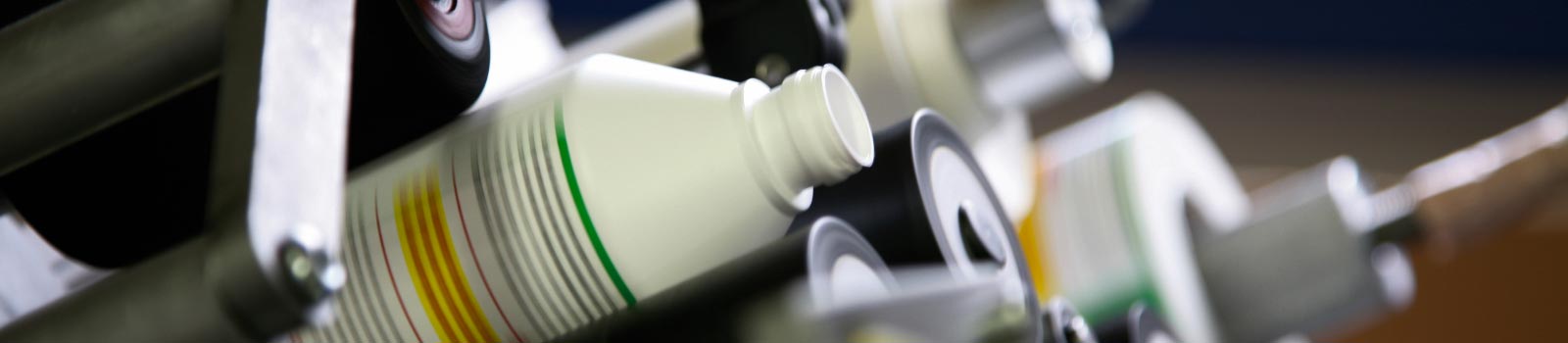
Modern industry demands precise, reliable and adaptable packaging and application solutions. Two-component cartridge systems meet these requirements, offering innovative solutions for a variety of sectors. These systems enable two components to be stored, mixed and applied separately, ensuring optimum use of reactive chemicals.
System A: a technology in transition
System A, long appreciated for its versatility in a variety of industrial applications, is currently in a transitional phase. This two-component cartridge system, which has effectively served the automotive, construction and electronics sectors, is gradually being supplemented by System B, considered to be much more advanced.
What are the advantages of System B?
The Bsystem, the improved successor to the A system, is the new benchmark for demanding industrial applications. This two-component cartridge system combines robustness and reliability, offering an advanced packaging solution particularly appreciated in sectors requiring high precision and consistent performance.
Main industrial applications of System B
- Chemical industry: packaging of epoxy resins and polyurethanes
- Medical sector: preparation of biomaterials and dental compounds
- Renewable energy industry: assembly of wind turbine and solar panel components
- Building and civil engineering: chemical anchoring systems and structural repairs
Benefits for users :
- Increased precision: System B 's design ensures homogeneous and precise mixing of components
- Waste reduction: controlled application minimizes product waste
- Ease of use: intuitive locking system simplifies cartridge changes
- Versatility: adaptable to a wide variety of products and applications
- Extended shelf life: efficient separation of components preserves their integrity
The B system meets the needs of industries looking for a reliable, high-performance packaging solution for their two-component products. Its advanced design and versatility make it the preferred choice for technical and high-precision applications, consolidating its position as the natural successor to the A system.
System C: a transition to more advanced solutions
The C system, known for its ability to handle large volumes in large-scale industrial applications, is currently in a transition phase. This two-component cartridge system, which has long served the automotive, aeronautical and construction industries for intensive use, is gradually being replaced by the more innovative F system.
The F system, versatile in its precision
The Fsystem, the improved successor to the C system, is the leading solution for complex industrial applications requiring high flexibility and precision. This two-component cartridge system offers an innovative design particularly suited to applications requiring fine control of mixing and application.
Common industrial applications
- Electronics: encapsulation of sensitive components
- Optics: precision bonding for lenses and prisms
- Medical industry: manufacture of implantable devices
- Aerospace: assembly of lightweight composite structures
- 3D printing: production of bi-material parts
Advantages for specific applications :
- Extreme precision: the design of the F system allows micron-level control of dosing and mixing
- Adaptability to sensitive materials: suitable for reactive or moisture-sensitive products
- Ease of integration: adapts easily to automated production systems
- Reduced air bubbles: optimized design minimizes the incorporation of air during mixing
- Heating capability: some models allow components to be preheated to adjust viscosity
The F system meets the requirements of high-tech industries industries requiring exceptional precision and reliability. Its versatility and performance make it the preferred choice for the most delicate applications, where mixing quality and repeatability are paramount, while offering a more advanced solution than its predecessor, the C system.
The K system: small but precise
The K system system stands out for its miniaturization and precision, offering a unique solution for applications requiring highly accurate dosing of small volumes. This two-component cartridge system is particularly well suited to industries where precision and economy of materials are crucial.
Typical K-system industrial applications
- Microelectronics: bonding miniature components
- Watchmaking: assembly of high-precision mechanisms
- Optics: coating contact lenses
- Biotechnology: reagent dosing for diagnostic tests
- Semiconductor industry: chip encapsulation
Comparative advantages :
- Saves materials: significantly reduces waste of expensive products
- Unrivalled precision: for applications down to the microliter level
- Repeatability: ensures consistent dosing, essential for high-precision industrial processes
- Versatility: adapts to a wide range of viscosities, from liquids to pastes
- Ease of use: intuitive system for quick cartridge changes
The K system meets the specific needs of high-tech industries where miniaturization and precision are paramount. Its ability to handle very small volumes with remarkable accuracy makes it an indispensable tool for the most demanding applications in terms of dosing and mixing bi-components.
How does Etraves use these cartridge systems?
Etraves, the contract packaging specialist, integrates two-component cartridge systems into its cartridge systems into its range of services to meet the specific needs of its industrial customers.
The company is focusing primarily on B, F and K systems, while maintaining its ability to manage A and C systems for existing customers.
Customized solutions are at the heart of Etraves' approach. The company selects the most appropriate system (B, F or K) according to thecustomer's specific application , and adapts mixing volumes and ratios accordingly. Thanks to its state-of-the-art equipment, Etraves ensures precise cartridge filling in strict compliance with quality and safety standards. Etraves' technical expertise enables us to assist customers in choosing the optimum system, be it the B system for demanding industrial applications, the F system for uses requiring great flexibility, or the K system for precision dosing in small volumes.
Etraves' production flexibility, capable of handling small and medium-sized production runs, enables it to adapt rapidly to variations in demand. This approach brings significant added value: customers benefit from cutting-edge technical expertise, reduce costs by outsourcing packaging, and enjoy consistent quality assured by rigorous controls. For customers still using A and C systems, Etraves continues to offer support, while guiding them towards the more advanced B and F system solutions where appropriate. This gradual transition enables customers to benefit from the latest innovations while maintaining continuity of operations.